
Customized High-Performance Components: LZH’s Laser Innovations
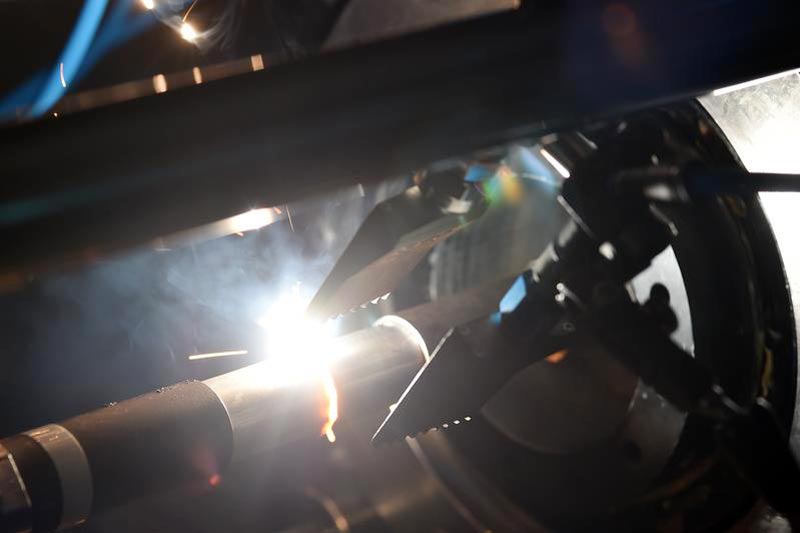
The ultrasonic-assisted laser beam welding process enables LZH scientists to produce crack-free, formable hybrid semi-finished products.
Photo: LZH
LZH researches laser processes for formable hybrid components.
Using expensive materials on high-performance components only where they are needed: This is the vision of the Collaborative Research Centre SFB 1153 “Tailored Forming”. Scientists at the Laser Zentrum Hannover e.V. (LZH) are researching two laser-based processes.
Hybrid semi-finished products can save material and costs in production if only those parts of a component are made from a high-priced material that is subject to high demands in later use and therefore has to be particularly wear-resistant, for example. The Collaborative Research Centre SFB 1153 “Tailored Forming” is developing a novel process chain for the production of load-adapted hybrid solid components in which the semi-finished products are first joined and then formed. To this end, the LZH is conducting research on two laser-based processes.
Formable semi-finished products manufactured by US laser beam welding
The Joining and Cutting of Metals group was able to produce crack-free formable semi-finished products using an ultrasonic-assisted laser beam welding process. The scientists welded shafts made of various mixed compounds such as steel-steel or steel-nickel and developed corresponding processes. The focus was on how cracks can be avoided and which parameters in the welding process influence quality characteristics such as weld penetration depth or weld reinforcement.
In the third funding period of the Collaborative Research Centre, the group wants to ensure greater process stability by modulating the laser power, among other things, and to develop process control to achieve repeatable, reliable quality in producing semi-finished products. In addition, mechanical stresses in the component are to be reduced by ultrasonic post-treatment.
Laser deposition welding takes local stress into account for components
The Machines and Controls group is conducting research into novel components with local, load-adapted property profiles. To this end, the scientists have used laser hot-wire deposition welding to apply a cost-intensive, high-strength material as a coating specifically to areas of the component that are subjected to high loads during operation. Exemplary applications are tooth flanks of gearwheels. In this way, high-quality and hard coatings could be applied, and the properties of the coating were specifically influenced by the material selection.
The LZH manufactures hybrid semi-finished products using laser deposition welding within the framework of the Collaborative Research Centre 1153 “Tailored Forming”. Photo: LZH
In the next step, the group would like to develop process monitoring for quality assurance in deposition welding. For this purpose, the secondary radiation generated in the welding process is to be measured with special sensor technology and analyzed with machine learning methods to be able to derive a prediction of the coating properties. The goal: non-destructive quality control of the coatings in the process.
About the Collaborative Research Centre
The work of the LZH is part of the Collaborative Research Centre SFB 1153 “Process chain for the production of hybrid high-performance components through tailored forming”, in which experts from nine institutes of the Faculty of Mechanical Engineering at Leibniz University Hannover, from the LZH and the Institute for Integrated Production Hannover IPH are working on developing new process chains for the production of hybrid components.
Within the SFB, the LZH is working on subproject A03 “Ultrasound-assisted laser welding for the generation of formable mixed compounds”, together with the Institute of Dynamics and Vibration (IDS), and subproject A04 “Spatial adaption of material properties of forming parts using surfacing techniques to produce graded hybrid components”, together with the Institute of Materials Science (IW).
The SFB started its work in July 2015. The third funding period runs for 4 years and starts in July 2023. It is funded by the German Research Foundation under the funding code 252662854.
Weitere Informationen:
More information about the Collaborative Research Centre 1153 is available on the Website of Leibniz University Hannover at https://www.sfb1153.uni-hannover.de/en/