
Cloud Automation: Controlling 100 Lasers at RWTH Aachen
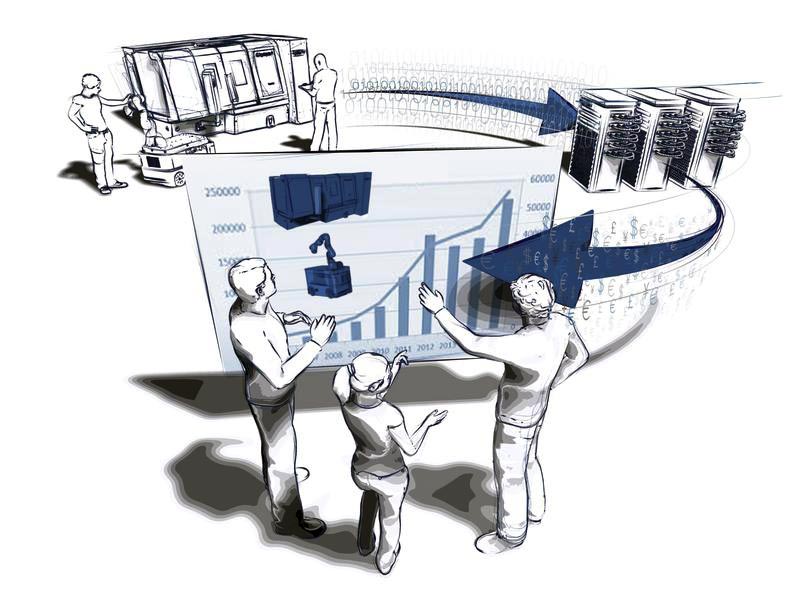
Mit Kubernetes lassen sich frei skalierbare Produktionssysteme steuern.
© Dr. Martin Riedel / Internet of Production
In the Cluster of Excellence “Internet of Production” (IoP), 200 scientists at RWTH Aachen University in cooperation with Fraunhofer ILT have set up a data center for controlling and monitoring industrial processes. The concept for this is based on a project for controlling laser systems developed at the Fraunhofer Institute for Laser Technology ILT and uses the open source software Kubernetes. A corresponding system has been running successfully at the institute for two years, and with it the institute can automatically and remotely install the software for new lasers in just a few minutes.
The task: setting up complex laser systems efficiently
An ultrashort pulse (USP) laser is a complex system that can ablate almost any material with micrometer precision. Numerous sensors control the machine and guide the laser process. The software that controls the components and reads the data from the sensors is accordingly diverse. In industrial production, many such systems are often used in parallel, and it is not uncommon to have 50 of them side by side. But how can their software be installed efficiently? And how can they be controlled centrally?
The solution: starting from scratch
Moritz Kröger, a research associate at the Chair for Laser Technology LLT at RWTH Aachen University, an associated chair at Fraunhofer ILT, was faced with precisely this question: “With the current programmable logic controllers, you can control one device quite well, but hardly a dozen or even 100 at the same time.” In this context – of controlling 50 to 100 lasers – conventional concepts would foreseeably not be sufficient for installing new software for these systems and evaluating sensor data in real time.
The solution? “We completely reprogrammed the machine control system,” reports Kröger. “This allowed us to rely on proven open source software right from the start, which gives us more compatibility and development options for distributed systems.” This way, the institute is able to control and optimize laser processing operations that must take into account, for example, data from the scanner controls, sensor data from different sources and analysis data during the ongoing process. The project started in 2018, and the control system is now running stably in the beta phase at Fraunhofer ILT.
At the core of the data center is Kubernetes, open source software that can automatically install, scale and maintain application programs on distributed computing systems. Kubernetes was originally designed by Google and is supported by leading cloud platforms including Microsoft Azure, IBM Cloud, Red Hat OpenShift, Amazon EKS, Google Kubernetes Engine and Oracle OCI.
Distributed computing for the automated manufacturing of the future
The potential has been recognized at RWTH Aachen University. As early as 2019, the concept was adopted by the Fraunhofer ILT for a data center at the university. In the Cluster of Excellence “Internet of Production”, engineers are working on the digitalization of manufacturing technology. Their goals are to increase and simplify cross-domain collaboration as well as to securely bundle all relevant data from many different sources in real-time, and all in the context of cyber-physical systems and the Fourth Industrial Revolution.
More than 35 university and non-university research institutions as well as the three Fraunhofer Institutes – FIT, ILT and IPT – are involved. More than 50 companies and associations are represented on the advisory board. They come from the automotive and aerospace industries, mechanical and plant engineering, as well as from the software sector.
Both in the Data Center of RWTH Aachen University and at Fraunhofer ILT, the systems are in use and are continuously being refined. The automated distribution of software and analysis of applications in the USP laser systems works reliably. “In five minutes, we can implement the software and hardware connection for a new laser, including integration into the cloud-based environment,” Moritz Kröger explains the current status. Research is currently being conducted into the automatic evaluation of measurement data. The goal is to combine data from as many systems as possible and have it graphically prepared for users. In the future, the process on the laser systems is to be optimized from the data in the field of artificial intelligence via machine learning.
The Cluster of Excellence “Internet of Production” (IoP) is funded by the German Research Foundation DFG. The first runtime phase started in January 2019 and will last seven years.
More information:
www.iop.rwth-aachen.de
“AI for Laser Technology Conference”
For further information on the use of artificial intelligence methods in industry and research will be available to interested parties at the virtual “AI for Laser Technology Conference” held by Fraunhofer ILT from September 28 to 29, 2021.
Details and registration: https://s.fhg.de/pij
Wissenschaftliche Ansprechpartner:
Moritz Kröger M.Sc.
Fundamentals of Melting Processes
Telephone +49 241 8040-433
moritz.kroeger@llt.rwth-aachen.de
Chair for Laser Technology LLT
RWTH Aachen University
Dipl.-Ing. Peter Abels
Group Manager Process Control and System Technology
Telephone +49 241 8906-428
peter.abels@ilt.fraunhofer.de
Prof. Dr.-Ing. Arnold Gillner
Competence Area Manager Ablation and Joining
Telephone +49 241 8906-148
arnold.gillner@ilt.fraunhofer.de
Weitere Informationen:
http://www.ilt.fraunhofer.de/en.html
http://www.iop.rwth-aachen.de