
Enhancing Laser Material Deposition with 3D Powder Gas Insights
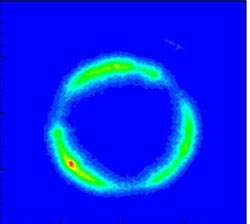
The powder gas feed is an important parameter of the overall process and plays a key role in the results achieved. Precise knowledge of the powder gas stream is therefore necessary to maintain process quality.
Laser material deposition has become an established processing technique for the repair and manufacture of metal parts and the functionalization of metal surfaces. A nozzle is used to inject a powdered filler material into the melt generated by the laser beam. This produces a layer which is metallurgically bonded to the workpiece. The delivery of powder to the melt pool via the nozzle is a crucial element in this process. It has a major influence on the consumption of powder material, the effectiveness of the gas shielding system used to prevent oxidation, and the quality of the coating layer. In order to ensure consistently high process stability and quality, it is necessary to check the processing results at regular intervals.
This is because nozzle wear can lead to deviations that cause changes in the diameter and position of the powder focus. Orientation of the powder gas stream to the laser beam is of major importance. Until now, the only way of determining these changes was to use laser metal deposition to obtain reference samples. Correlating these samples with comparative deposited welds revealed the quality of the nozzle.
A simpler method of checking nozzle quality
A team from the Fraunhofer ILT has now developed a measurement procedure for characterizing the powder gas stream which provides a simple and reproducible means of checking nozzle quality. The process involves illuminating the powder gas stream from the side with a laser beam and using a camera positioned coaxially to the nozzle to capture images of the powder gas stream through the nozzle. This makes the ring-shaped distribution of the powder visible. Thanks to the camera's high frame rate, it is possible to precisely determine the number and position of individual powder particles at a defined point in time. Based on similar principles to laser caustic measurement, the lateral laser beam moves down the powder gas stream layer by layer, requiring just a few seconds to capture the data for each layer. The system then calculates the particle density distribution for each layer from the several thousand individual images captured by the camera. Finally, the individual layer images are superimposed on each other to yield the overall spatial particle density distribution. “For the first time, we have succeeded in developing a measuring procedure that enables us to determine the constancy of the powder mass flow, the symmetry of the powder gas stream, and the position and size of the powder focus,” says Stefan Mann, who is in charge of the project at the Fraunhofer ILT. Potential applications of this new measuring technique include all activities in the field of laser deposition welding, in particular engine and power plant manufacturing, toolmaking and mechanical engineering.
Live demonstration of the measuring process
A demonstration of this measuring procedure will be held in the Fraunhofer ILT’s laser equipment facility in Aachen on May 11 as part of the “Laser Technology Live” event at the International Laser Technology Congress AKL’12. To find out more, please visit www.lasercongress.org
Your contacts at Fraunhofer ILT
Our experts are on hand to answer your questions:
Dip.-Ing. Stefan Mann
Process Control and System Technology
Phone +49 241 8906-321
stefan.mann@ilt.fraunhofer.de
Dipl.-Ing. Peter Abels
Head of Process Control and System Technology
Phone +49 241 8906-428
peter.abels@ilt.fraunhofer.de
Fraunhofer Institute for Laser Technology ILT
Steinbachstrasse 15
52074 Aachen
Phone +49 241 8906-0
Fax +49 241 8906-121