
New Inline Measurement System Boosts Flat Film Production Efficiency
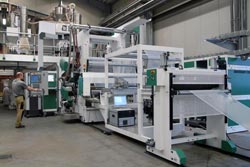
In 2011, the German plastics processing industry generated revenues of 55.9 billion euros, up 15 percent on the previous year's figure. Approximately one third of these revenues were generated by the packaging industry, which makes more than half of its sales from extruded packaging systems.
As demand increases, so too does the complexity of the plastic packaging solutions requested by customers – and this challenge is pushing manufacturers to place more and more emphasis on functionalizing packaging films by offering complex layer structures. For example, adding a layer of ethylene vinyl alcohol (EVOH) copolymers creates a diffusion barrier against oxygen and water vapor which ensures that food products keep fresh longer. Currently, the minimum thickness of individual functional layers lies between 2 – 100 µm. In order to ensure they meet the minimum thickness requirements, plastics manufacturers apply more of the expensive functional material than is strictly necessary. As a result, EVOH and comparable plastics such as polyamide (PA) have come to represent a significant cost factor.
Guaranteeing quality and reducing material waste
The challenge faced by manufacturers of multilayer films is to make the functional layers thick enough without using excessive amounts of material. This is where a film inspection system can make a real difference: The system's measuring beam is moved diagonally across the film from one side to the other and takes a series of readings which enable it to determine the thickness of each individual layer. The sensor is capable of measuring multiple layers simultaneously at production speed. A software program analyses the data and triggers an alert if the readings deviate from the target thicknesses. This enables the manufacturer to correct the ongoing process immediately after detecting an out-of-tolerance reading and to maintain quality by either reducing or increasing the quantity of material used in response to the inline measurements. There is currently no other tool on the market capable of performing these inline measurements.
A further benefit of the film inspection system relates to the even distribution of the functional layer across the film's entire width. The nature of the production process means that the functional layer gets thinner towards the edge. As a result, manufacturers are forced to remove the edges of the film on both sides, representing a significant waste of material. Minimizing this wastage is an important issue. The inline measurement system makes it possible to determine precisely where this critical drop-off in thickness begins, thereby keeping wastage to a minimum.
Measurement system suitable for continuous use
Under the coordination of Stefan Hölters from Fraunhofer ILT and Janina Overbeck from the IKV, long-term measurements covering a period of more than 12 months have already been performed on blown films at the company A+C Plastic Kunststoff GmbH in Eschweiler, Germany. The results confirm that the measurement system is suitable for long-term, continuous use. The »VenPad« measuring system developed by the project partner Octagon Process Technology GmbH kept the measuring conditions constant and ensured that the results were accurate at all times. The experts have now applied these results to flat films: Under close-to-real-life manufacturing conditions, they successfully operated the measurement system in a series of tests run over a period of several days at the plant engineering firm Kuhne GmbH in Sankt Augustin.
Contacts
Dipl.-Phys. Stefan Hölters MBA
Head of the Group Clinical Diagnostics and Microsurgical Systems
Phone +49 241 8906-436
stefan.hoelters@ilt.fraunhofer.de
Fraunhofer Institute for Laser Technology ILT
Steinbachstraße 15
52074 Aachen
Assistant Professor Dr. Reinhard Noll
Head of the Competence Area Measurement Technology and EUV Sources
Phone +49 241 8906-138
reinhard.noll@ilt.fraunhofer.de
Fraunhofer Institute for Laser Technology ILT
Steinbachstraße 15
52074 Aachen