
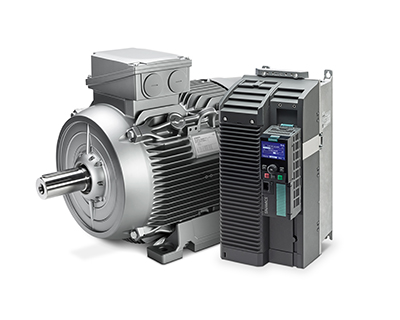
The Simotics reluctance motors with an aluminum or gray cast-iron enclosure cover an output range from 5.5 to 30 kW, achieving high levels of efficiency in full and partial load range.
- Integrated Drive System (IDS) comprising Simotics reluctance motors and Sinamics converters for cost-effective, efficient plant operation
- High levels of efficiency in full and partial load range
- High dynamic response and speed consistency for precise control
- Output range from 5.5 to 30 kilowatts (kW)
Siemens is extending its portfolio of Integrated Drive Systems (IDS) with a new drive series featuring synchronous reluctance technology, characterized by very high levels of efficiency.
Reluctance motors and converters are specially designed to work together as an Integrated Drive System, enabling particularly efficient operation. Predefined parameters in the form of a code on the motor type plate simplify the commissioning process.
The new drive series is based on the proven Simotics 1LE1 motor platform, and is designed to interoperate with the Sinamics G120 converters. The Simotics reluctance motors cover an output range from 5.5 to 30 kW and are available either with an aluminum enclosure for general operating conditions (Simotics GP) or with a gray cast-iron enclosure for more aggressive operating conditions (Simotics SD). The synchronous principle means that the speed remains constant, and sensorless vector control ensures optimum performance. Both features enhance the controllability of the drive system. Ramp-up times are short thanks to the motor's low inherent moment of inertia combined with the vector control. The low losses in the rotor result in a high thermal utilization of the motor. In terms of its design and handling, the motor is similar to the 1LE1 asynchronous motors.
The Sinamics G120 standard converter incorporates vector control designed specifically for reluctance motors. The identification of the pole positions prevents jerking movements of the drive on activation, while a flying restart enables synchronization with the running motor. As part of the Totally Integrated Automation (TIA) concept, the drive series is integrated into the automation environment via Profibus and Profinet interfaces.
The reluctance technology is used in process engineering with pumps, fans, compressors, mixers and centrifuges, in materials handling applications, and in the mechanical engineering sector.
The Simotics reluctance motors with an aluminum or gray cast-iron enclosure cover an output range from 5.5 to 30 kW, achieving high levels of efficiency in full and partial load range.
For further information on motors, visit www.siemens.com/reluctance-drive-system
Siemens AG (Berlin and Munich) is a global technology powerhouse that has stood for engineering excellence, innovation, quality, reliability and internationality for more than 165 years. The company is active in more than 200 countries, focusing on the areas of electrification, automation and digitalization. One of the world's largest producers of energy-efficient, resource-saving technologies, Siemens is No. 1 in offshore wind turbine construction, a leading supplier of combined cycle turbines for power generation, a major provider of power transmission solutions and a pioneer in infrastructure solutions as well as automation, drive and software solutions for industry. The company is also a leading provider of medical imaging equipment – such as computed tomography and magnetic resonance imaging systems – and a leader in laboratory diagnostics as well as clinical IT. In fiscal 2014, which ended on September 30, 2014, Siemens generated revenue from continuing operations of €71.9 billion and net income of €5.5 billion. At the end of September 2014, the company had around 357,000 employees worldwide. Further information is available on the Internet at www.siemens.com
Reference Number: PR2015020119PDEN
Contact
Mr. Stefan Rauscher
Process Industries and Drives Division
Siemens AG
Gleiwitzer Str. 555
90475 Nuremberg
Germany
Tel: +49 (911) 895-7952
stefan.rauscher@siemens.com