
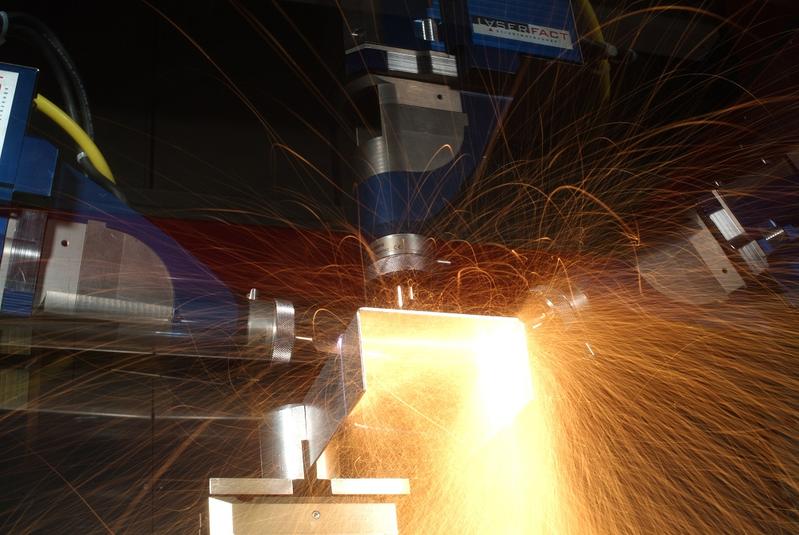
Laser combi-head for cutting and joining as well as additive manufacturing by means of laser metal deposition.
Fraunhofer ILT, Aachen.
Together with project partners from science and industry, scientists from the Fraunhofer Institute for Laser Technology ILT have advanced the development in separation and joining as well as heat treatment technologies. They will present selected results at the EuroBLECH from October 25 to 29 in Hanover, Germany (Hall 11, joint Fraunhofer Stand B135).
Laser Processing of Ultra-high Strength Steels
Sheets made of ultra-high strength steels are commonly used for B-pillars or side door sills of passenger cars, where an extremely high absorption of kinetic energy is a key issue in the event of an impact. However, the high strength of these materials makes it necessary to adjust the processing methods, such as cutting and joining. Conventional mechanical cutting and joining processes, such as stamping, clinching or riveting, cannot be used at a reasonable expense.
As an alternative, the tool “light” has proven its value as a processing method in industrial applications. Laser cutting has already proven itself many times as a separation process, while joining is essentially achieved by spot welding. Both methods, however, lead to metallurgical effects that can adversely affect the component properties. During cutting, hardening occurs in the edge zone of the cut edge; in the case of spot welding, a heat-affected zone forms with a distinct hardening reduction around the welding spot.
These two effects lead, in the worst case, to the failure of the joint and thus, in the case of damage, to a reduced absorption of the kinetic energy in the component. By means of local laser heat treatment in the cutting edge region and in the joining zones, this weakening can be counteracted. The hardness and ductility of the material can thus be adjusted locally to tensile elongations of 10 to 15 %.
Joining ultra-high strength materials requires a low energy per unit length. This can be achieved with laser welding at 20 to 80 kJ/m. For thin plates of chromium steels with martensitic microstructure and tempering steels, suitable fusion welding parameters have been developed at Fraunhofer ILT. TWIP steels containing high content of manganese have also been successfully joined by laser welding in joints with the same as well as with dissimilar materials. A loss of the strength was countered here by a suitable load control.
Laser Combi-heads for the Processing of Car Body Components
Last but not least, it makes sense to combine individual process steps in one tool for economic reasons. This is the starting point of the collaborative project KLASSE, sponsored by the German Federal Ministry of Education and Research (BMBF); the project is being carried out by the Fraunhofer Institute for Laser Technology ILT along with partners from the automotive industry and laser plant construction. The work in “KLASSE” has resulted in a combined processing head with a hybrid laser beam source consisting of a diode laser for heat treatment and a fiber laser for cutting.
For several years now, a laser processing head developed by Fraunhofer ILT and marketed by Laserfact GmbH has been successfully used in the industry, combining different work steps. The head incorporates the two process steps “cutting” and “welding” into one machine without a need for retooling. In the spring of 2016, a powder nozzle was integrated into the combi-head, enabling it to carry out additive manufacturing steps by means of laser metal deposition.
Thanks to this integration, set-up times can be minimized and highly flexible production made even more efficient. In addition, the combi-head can also be used to cut composite materials, e.g. carbon-fiber reinforced components, which are becoming increasingly popular in car body manufacturing due to their low weight and excellent mechanical properties.
Local Softening of Cold-rolled Steels
After cold-rolling, cold-strengthened steels are generally subjected to overall recrystallization annealing. In the cold-strengthened state, the thickness of the steel sheets can be reduced, but the material can only be deformed to a lesser degree, and its ability to absorb energy – in the event of a crash – is reduced significantly. A local heat treatment can improve the crash properties of the components (e.g. controlled folding of a crash box) by introducing soft zones into it. In sheet-metal plates made of low-alloy steels, a combination of cold rolling and local laser heat treatment prevents cracks from occurring in the subsequent forming process at particularly stressed areas, typically at the edges of shaped components.
The project “Local Laser Heat Treatment of Cold Strengthened Steels for Improvement of Forming and Functional Characteristics” (LAKS) is being funded by the German Federation of Industrial Research Associations (AiF) and carried out at Fraunhofer ILT and the Metal Forming Institute (IBF) at RWTH Aachen University. Based on parameter studies, the institutes are first determining correlations between the temperature-time profiles and the resulting properties and mechanical properties. Subsequently, deformation tests and crash tests shall be carried out. The latter will be validated in forming tests under quasi-static as well as under sudden loads. In future development steps, the institutes shall investigate corrosion properties, simulate the deformation in production and operation as well as arrange the process into the production process optimally.
Contact
Dr. Andreas Weisheit
Head of Group Cladding and Heat Treatment
Phone +49 241 8906-403
andreas.weisheit@ilt.fraunhofer.de
Dr. Dirk Petring
Head of Group Macro Joining and Cutting
Phone +49 241 8906-210
dirk.petring@ilt.fraunhofer.de
Fraunhofer Institute for Laser Technology ILT
Steinbachstraße 15
52074 Aachen, Germany