
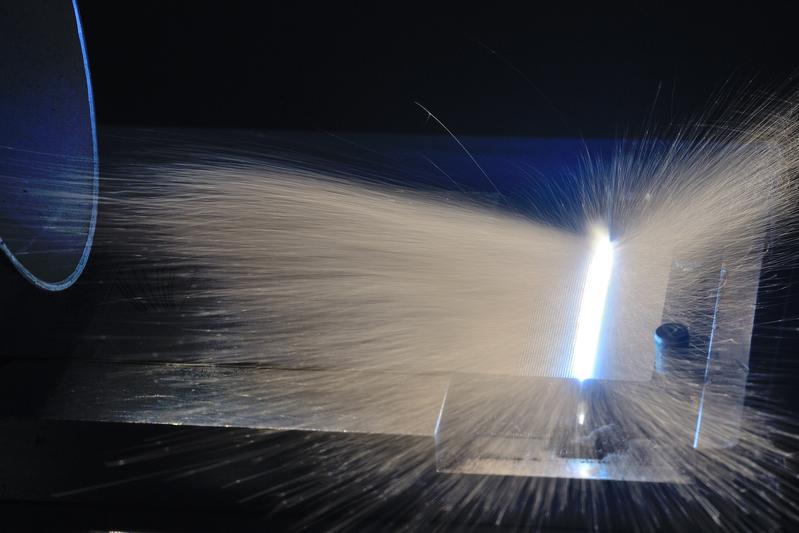
Image 1: Structuring a metal probe with a high-power fiber laser in preparation for a metal-plastic bond.
© Fraunhofer ILT, Aachen, Germany.
K is the world’s largest trade fair for the plastics and rubber industry. As in previous years, the organizers are expecting 3,000 exhibitors and more than 200,000 visitors from around the world. Focus topics this year include industry 4.0, resource efficiency, new materials and lightweight design.
Isotropic joining of plastic and metal
A key factor in lightweight design is the ability to form positive and permanent bonds between metallic and plastic surfaces. There is actually already a known laser method for this, particularly for fiber composite materials used in the aerospace and automotive industries.
The method involves first structuring the metal surface with the laser, then bonding it with the heated plastic surface. Previously, the laser structuring was done in a scanning process that produces lines on the metallic surface.
As part of the HyBriLight project funded by Germany’s Federal Ministry of Education and Research (BMBF), specialists at Fraunhofer ILT developed a new process for structuring that uses an ultrashort pulse (USP) laser, which produces cone-like protrusions (CLP) on the metal. These randomly distributed micro-elevations increase the surface area five- to tenfold.
As a result, the bond is not only stronger, but also equal in all directions because, unlike with the scan lines, the surface now has an isotropic structure. The process has been tested in the lab and also works for injection molding with metallic inserts. This method will also be on display with a large demonstrator (image) at K 2016.
Absorber-free laser transmission welding
When laser welding thermoplastics, one of the components is usually transparent, and an absorber material is added to the second part to enable it to better absorb the laser radiation. The laser then passes through the first component and melts the second, thus joining the two parts.
The additive can be omitted if a longer-wavelength laser is used. Then both components absorb the radiation and care must be taken to ensure selective melting while minimizing the size of the heat-affected zone (HAZ). The process required for this was developed at Fraunhofer ILT and involves rapidly (>1 m/s) and repeatedly guiding the laser beam along the welding contour while simultaneously discharging the heat above and below the parts being joined.
The method is expected to be of interest particularly in the field of medical engineering, where additives can pose a risk to biocompatibility. However, the method can also be used in other applications where absorbers are not permissible for reasons of appearance, cost or function.
Secure and gentle sealing of multilayer films
A similar laser can also be used to seal multilayer films against external media. This is useful, for example, when processing lithium batteries or OLED displays, which contain materials that are very sensitive to oxygen or water vapor. For this reason, they are encapsulated in special high-barrier multilayer films.
Normally the film is adhesively bonded or heat-sealed around the perimeter of the components to be protected, creating a pocket that includes, for instance, the flexible organic LED. Now, with a special laser, it is possible to selectively melt just one layer of the film, making the production-ready sealing process even gentler for the packaged component.
In addition to its suitability for electronics, this technology could also be of interest in the area of medical packaging that has to satisfy stricter requirements. Developed as part of a research project, this technology is currently still being refined. Future plans for it include encapsulation of flexible solar cells and use in roll-to-roll processing.
Fraunhofer ILT will have several specialists in the development of new laser-based technologies and processes representing the institute at the joint Fraunhofer booth at K 2016, Hall 7, Booth SC01.
Contact
Dr.-Ing. Alexander Olowinsky
Group Manager Micro Joining
Telephone +49 241 8906-491
alexander.olowinsky@ilt.fraunhofer.de
Dipl. Wirt.-Ing. Christoph Engelmann
Micro Joining Group
Telephone +49 241 8906-217
christoph.engelmann@ilt.fraunhofer.de
http://www.ilt.fraunhofer.de/en.html