
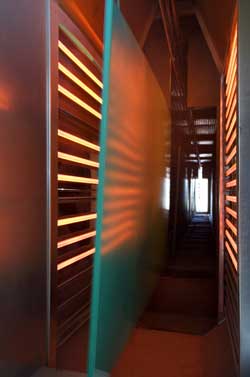
Hawes Signs offers design, manufacture, installation and maintenance of a comprehensive range of external and internal signs for customers ranging from high street banks to car dealerships and supermarket chains. The company’s advanced manufacturing facilities include the latest in digital printing, vinyl cutting and flexible machine tool technology, so that it is ideally suited to handle large volume roll-out programmes as well having the capability to meet lower volume customised requirements.
Naturally, finishing operations are vital to the production of high quality signage and environmentally-friendly powder coating is used to provide a sign surface which offers high gloss-retention and is highly resistant to chipping, scratching, fading and weatherability. The powder-coating facility at Hawes Signs uses epoxy/polyester/pigment powders which are sprayed directly onto predominantly steel and aluminium panels, of various sizes. This powder must then be brought to a temperature which allows it to flow and fuse before being cured for a given time.
Previously, the sprayed-on powder had been pre-heated by a gas-fired infrared system before entering a warm air convection oven for final curing. However, this oven was starting to cause maintenance problems and to eliminate unwanted line stoppages while, at the same time increasing line speeds, it was decided to investigate alternative powder pre-heating methods.
Extensive tests were carried out at Heraeus’ Neston Applications Centre and these showed that the powder coatings could be quickly and reliably heated to the required temperatures by medium wave, electric infrared. As a result, a purpose-built medium wave, infrared oven was conveniently retrofitted into the existing powder coating and curing line, between the coating cabin and the warm air oven. This consists of two parallel zones, a 50kW zone which heats the coated side of the panels and a 35kW zone which heats the rear, uncoated side of the panels to accelerate the heating effect. Each of the zones can themselves be switched between two power outputs to accommodate two sizes of panel.
Since installation, the oven has helped to speed up the powder coating process as it heats the powder faster than the old system and it has also reduced the cure dwell time in the convection oven. In addition, quality has improved, as the medium wave heaters provide a uniform flow and fusion of the powders.
Heraeus Noblelight GmbH with its headquarters in Hanau and with subsidiaries in the USA, Great Britain, France, China, Australia and Puerto Rico, is one of the technology- and market-leaders in the production of specialist light sources. In 2006, Heraeus Noblelight had an annual turnover of 88 Million € and employed 651 people worldwide. The organisation develops, manufactures and markets infrared and ultraviolet emitters for applications in industrial manufacture, environmental protection, medicine and cosmetics, research, development and analytical laboratories.
Heraeus, the precious metals and technology group headquartered in Hanau, Germany, is a global, private company in the business segments of precious metals, sensors, dental and medical products, quartz glass and specialty lighting sources. With revenues of more than EUR 10 billion and more than 11,000 employees in over 100 companies, Heraeus has stood out for more than 155 years as one of the world’s leading companies involved in precious metals and materials technology.
Hawes Signs is part of ECCE International, a unique global signage company owned equally by Hawes (UK), Kubald (Germany) and Rousseau (France).
Further Information:
Readers:
Heraeus Noblelight GmbH
Reinhard-Heraeus-Ring 7
D-63801 Kleinostheim
phone +49 6181/35-8545, fax +49 6181/35-16 8545
E-Mail hng-infrared@heraeus.com
Press:
Dr. Marie-Luise Bopp
Heraeus Noblelight GmbH,
phone +49 6181/35-8547, fax +49 6181/35-16 8547
E-Mail marie-luise.bopp@heraeus.com