
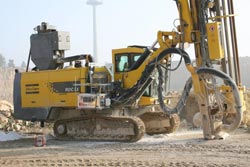
The most common methods for mining mineral reserves are drilling, blasting and cutting. In order to decide which areas are worth mining, a mine operator needs to be able to model the deposit accurately, showing where, at what depth and at what concentration the desired ore is to be found. This not only avoids the pointless mining of worthless rock, it also saves the mine operator time and money in resource extraction.
Currently, the information required for the detailed modeling of a deposit is collected by core drilling: a core sample is taken from underground and sent to a laboratory, and the composition of the drilled rock is then determined using X-ray flourescence (XRF) analysis. The mine operator has to wait three to five days to receive the information. This method is the state of the art.
Because core drilling is time-consuming, mining companies are keen to see the development of a quicker analysis method that still offers sufficiently detailed information. As part of the InnoNet project OFUR – Online Analysis for Minerals Extraction – funded by the German Federal Ministry of Economics and Technology (BMWi), researchers from Fraunhofer ILT, in collaboration with the Institute for Mining and Metallurgy Machinery at RWTH Aachen University and seven partners from industry, have developed a robust demonstrator with an inline analysis module for use in mining. This directly analyzes rock as it is drilled: a 10-centimeter-diameter hole is drilled up to 24 meters deep into the rock using a conventional drilling rig that has been fitted with the analysis module. The system measures the chemical composition of the rock during drilling and makes the evaluated data available immediately. »The challenge of this project was to redesign the laser sensors so that they could withstand the operating conditions,« says Dr. Cord Fricke-Begemann, who heads up the Materials Analysis group at Fraunhofer ILT. »We’ve managed to develop measuring apparatus that can cope with extremes of temperature, strong vibrations, and high levels of moisture and dust.«
Real-time multi element analysis
The analysis method used is laser-induced breakdown spectroscopy (LIBS): the rock dust is drawn up to the surface through a hose and separated out by particle size using a cyclone. The mixture of dust and air travels through the hose at speeds of up to 20 meters per second, but it is during this journey that the actual analysis – which takes no more than 20 microseconds – is done. A high-energy laser pulse is focused on the passing dust particles. These are first vaporized and then turned into a plasma by the heat of the laser. For a brief period, the plasma radiates at a frequency that is specific to the elements it contains. The spectrometer simultaneously detects the radiation emitted by all the elements, and these data are sent to a computer for evaluation. During analysis, the laser pulse hits particles that are made up of different elements, and results are averaged for very short time periods. This provides useful information about the overall composition of the rock, whilst the chronology of the data sequence shows how the deposit is layered.
The decisive advantage of this method is its enormous time saving. Since the data are evaluated and presented in a matter of seconds, the mine operator can determine the quality of a deposit immediately and adjust the mining process accordingly. So far, this method has been used to detect magnesium, calcium, silicon, iron and aluminum. The researchers in Aachen have set themselves the challenge of soon being able to detect copper and other metals using a different spectrometer.
In the long term, this real-time procedure for multi element analysis should make it possible to automate extraction machinery. The Materials Analysis group and its partners have worked up a concept for how the system could be fitted to underground shearer loaders. Above ground, the demonstrator could be fitted to drilling rigs used for extracting mineral deposits. The inline analysis enables continuous quality control and rolling updates to the modeling of the deposit. Work has already begun on a follow-up project which aims to make the analysis system fit for industrial application. Drilling rigs with laser analysis capability would be a unique selling point for the medium-sized companies involved in the project and would open up new sales potential for them.
Contacts at Fraunhofer ILT
Our experts are happy to answer any questions:
Dr. rer. nat. Cord Fricke-Begemann
Materials Analysis
Tel. +49 241 8906-196
cord.fricke-begemann@ilt.fraunhofer.de
Dr. rer. nat. Reinhard Noll
Laser Measurement Technology
Tel. +49 241 8906-138
reinhard.noll@ilt.fraunhofer.de
Fraunhofer-Institut für Lasertechnik ILT
Steinbachstrasse 15
52074 Aachen
Tel. +49 241 8906-0
Fax. +49 241 8906-121