
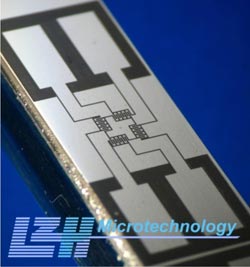
Laser structured strain gauges can be used for exact measurement of forces at critical points, such as for highly stressed tooling machines or complex 3-D workpieces. Currently, the Laser Zentrum Hannover (LZH) is developing sensor structures using ultrashort laser pulses, with the goal of making the production of high-quality thin-film strain gauges economically attractive for small and middle-sized batches.
Monitoring production for tooling machines, preventing overloading and lost work time, or controlling fuel injection in diesel motors are just a few examples for important uses of the so-called thin-film strain gauges (TFSG). They can be used for exact and real time measurement of strain in machines, bearings or motors, at the place where the highest strain occurs. However, these environments call for highly robust sensors which can withstand high temperature fluctuations as well as mechanical and chemical stresses.
Previous sensor solutions have distinct weaknesses. Often, TFSG foils are attached using adhesives, which can run or ooze, and thus distort measurement results. Especially in rough environments, the long-term stability of these sensors can be greatly impaired. Thus, strain gauges based on thin-film technologies are preferred for applications with special requirements. Photo-lithographic sensor structures are complex, and not cost efficient for small or middle-sized batches. Also, the masking techniques used in electronics production are not suitable for complex workpieces with cylindrical, spherical or free-form areas, and can thus only be used for flat workpieces.
The Production and System Technology Department of the LZH is working on a new solution. The Microtechnology Group of this department is currently working on developing a laser-structured TFSG. After the workpiece has been coated with an isolation and sensor layer, an ultra short pulse laser with a lateral resolution of 10 to 100 µm can be used to structure the sensor, without thermally damaging the sensitive layers. The advantage of using this process is that complicated masking processes are not necessary, and the sensors can be directly applied to complex, three-dimensional workpieces.
These developments are a part of the special research project “Gentelligent Components in their Lifecycle”, which is financed by the German Research Foundation. The main goal is to develop a multi-sensor network for monitoring processes, machines and workpieces, which gathers information and can make a prediction based on this. The first prototypes of a laser structured TFSG are planned for use in the z-axis slides of a tooling machine. Apart from machining, other possibilities for using the innovative surface sensor can be found in automotive technology, bearing technology, robotics or in medical technology (e.g. prosthetics).
A second project of the Microtechnology Group is concerned with developing a process which can be used for better coatings on complex surfaces. In cooperation with the Fraunhofer-Institute for Surface Engineering and Thin Films, investigationson the possibilities of using High Power Pulsed Magnetron Sputtering (HPPMS) or Modulated Pulse Plasmas (MPP) are being carried out.
Both methods can be used to improve the surface roughness of the deposition layer as well as for coating undercut areas. The MPP process also has the advantage that, apart from the improved layer characteristics, there is also a higher deposition rate than that of conventional sputtering methods. The results of the project “Directly Applied Thin-Film TFSG on 3-D Workpieces” will first be used in the area of precision weighing technology.
Contact:
Laser Zentrum Hannover e.V.
Michael Botts
Hollerithallee 8
D-30419 Hannover
Germany
Tel.: +49 511 2788-151
Fax: +49 511 2788-100
E-Mail: m.botts@lzh.de
The Laser Zentrum Hannover e.V. (LZH) carries out research and development in the field of laser technology and is supported by the Ministry of Economic Affairs, Labour and Transport of the State of Lower Saxony (Niedersächsisches Ministerium für Wirtschaft, Arbeit und Verkehr).