
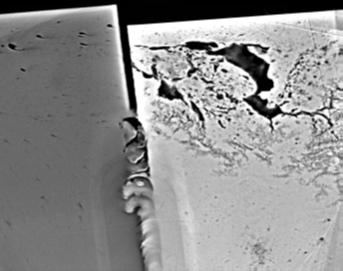
X-ray image of a FSW seam
Fraunhofer IZFP
Fraunhofer IZFP researchers aim for process-integrated inspection of the error-prone seam zones of friction stir welded components. In doing so, they significantly contribute to the reduction of costs and wastage at concurrent saving of time.
As a novel, forward-looking joining technology, Friction Stir Welding (FSW) is an easily applicable, clean and innovative process especially suited for light metals and increasingly applied in automotive industry, machine construction and aerospace engineering. Unlike most conventional joining techniques it enables considerable weight saving, thus complies the goals of lightweight construction.
In order to extend existing application limits, a variant of FSW called “Ultrasound-Supported Friction Stir Welding” (US-FSW) was developed. To guarantee a steadily high quality of weld seams and to identify possible process fluctuations, the application of nondestructive inspection methods is indispensable for both variants: Quality has to be ensured during all phases of the process and defects or imperfections with possibly negative impact on the weld seam durability – such as pores and cracks – have to be detected.
Concerning nondestructive testing (NDT), FSW is subject to similar principles as conventional welding procedures. The application of high-performance, reliable and cost-efficient NDT to assess the quality of the produced joints enables a considerable extension of FSW’s application range.
“The spectrum of procedures provided at Fraunhofer IZFP allows to obtain a holistic view of the entire process. This goes much further than typical ways of inspection such as the post-process detection of irregularities. Our approach enables to increase efficiency even before and during the welding operation and to monitor the joining process. As a consequence we find greatly widened fields of application for FSW,“ Dr. Benjamin Straß, group leader within Fraunhofer IZFP’s “Production-integrated NDT” department, explains.
The research project is funded by the German Research Foundation DFG. Within the scope of this project, Fraunhofer IZFP‘ researchers develop methods to optimize process parameters, to detect possible defects in the joining area and to characterize alterations of the material properties of friction stir welded hybrid-joints.
“To our institute, such a fundamental research project offers the incentive to test and to develop new approaches which partially can be transferred to further production technologies. By this, new potential clientele can be attracted. Even beyond the boundaries of this project there is a regular communication and exchange of experiences between the research institutions in the priority program*. Hereby, new and interesting contacts arise regularly,“ Straß concludes.
http://www.izfp.fraunhofer.de/en.html