
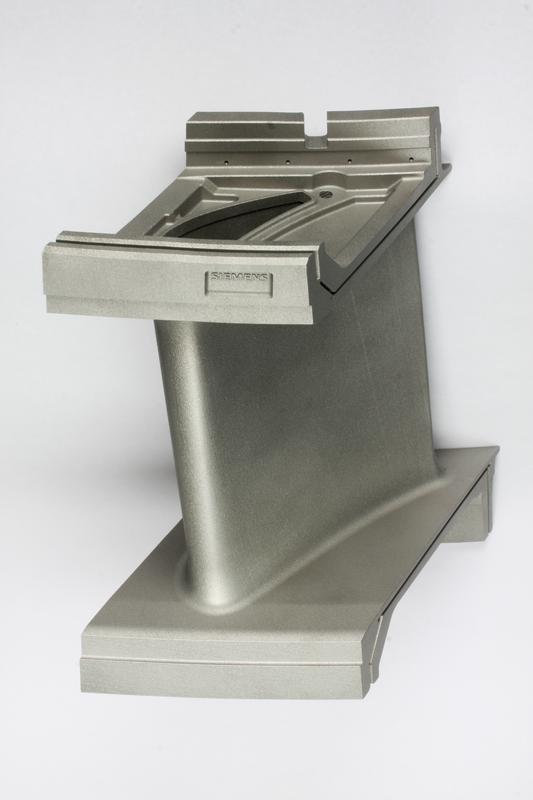
Guide vanes made using the new modular process chain (material: Inconel® 718).
Fraunhofer ILT, Aachen, Germany.
Last year, Siemens commissioned its Clean Energy Center, a new combustion test center in Ludwigsfelde near Berlin. The center plays a major role in developing and refining gas turbines as a facility for conducting realistic tests on various turbine components with liquid or gaseous fuels. Rigorously optimizing the combustion processes involved is the key to achieving greater energy efficiency in the turbines.
During the tests, individual turbine parts are exposed to temperatures of 1500 degrees Celsius or more. Such components are usually manufactured from superalloys in a precision casting process, in which each iterative loop may last several months and incur significant costs. Thus far, this has severely curtailed the number of tests possible.
Fast prototype production with additive laser techniques
Experts from the Siemens gas turbine manufacturing plant in Berlin and the Fraunhofer Institute for Laser Technology ILT in Aachen, Germany, have now developed a laser-based technology that considerably speeds up the manufacturing process for turbine vanes slated for the hot gas area of the engine.
To withstand the high temperatures over long periods of time, the turbine vanes require complex internal cooling structures. Selective laser melting (SLM) has proven itself to be up to the challenge, especially for prototypes or small batches featuring complex geometries. Similar to using a 3D printer, special alloys are melted by laser on a powder bed. The components are then built up layer by layer.
Over the past several years, Fraunhofer ILT has built up considerable expertise in the use of additive laser techniques and alloys for components exposed to high temperatures. With this wealth of experience, the scientists were able to develop special processes that made it possible to produce the relatively large parts (up to 250 mm) at Siemens with a high degree of dimensional accuracy and superior surface quality.
New production chain uses modular design for turbine vanes
Securely mounted on the turbine housing, guide vanes channel the hot gas to the movable rotor blades. The guide vanes consist of two massive platforms plus an airfoil with a delicate cooling structure. The latter presents a major manufacturing challenge; even production using SLM required additional internal supports.
A modified process chain has solved the problem: the platforms and the airfoil are manufactured separately and then subsequently brazed together. This makes it possible to not only eliminate the supports in the blade, but also to improve the surface quality. The result is a fully functional component that can be used in hot path rig testing in order to deliver quick feedback to the design engineers.
Siemens optimized various production steps in preparation for this idea. After manufacturing via laser, the parts are precisely measured, subjected to finishing, and then joined using high temperature brazing.
This modular production of turbine blades offers significant potential for other components as well. It would make it possible to connect cast and SLM-made parts, leaving just the complex or variable parts to be produced using SLM. At the same time, it would also facilitate the production of parts with difficult geometries that are currently too large for the SLM process.
Contact:
Dipl.-Ing. Jeroen Risse
Group Rapid Manufacturing
Telephone +49 241 8906-135
jeroen.risse@ilt.fraunhofer.de
Dr.-Ing. Wilhelm Meiners
Group Manager Rapid Manufacturing
Telephone +49 241 8906-301
wilhelm.meiners@ilt.fraunhofer.de
Fraunhofer Institute for Laser Technology ILT
Steinbachstraße 15
52074 Aachen, Germany
http://www.ilt.fraunhofer.de/en.html
http://s.fhg.de/BYt