
Aachen Center for Additive Manufacturing Gains Industry Praise
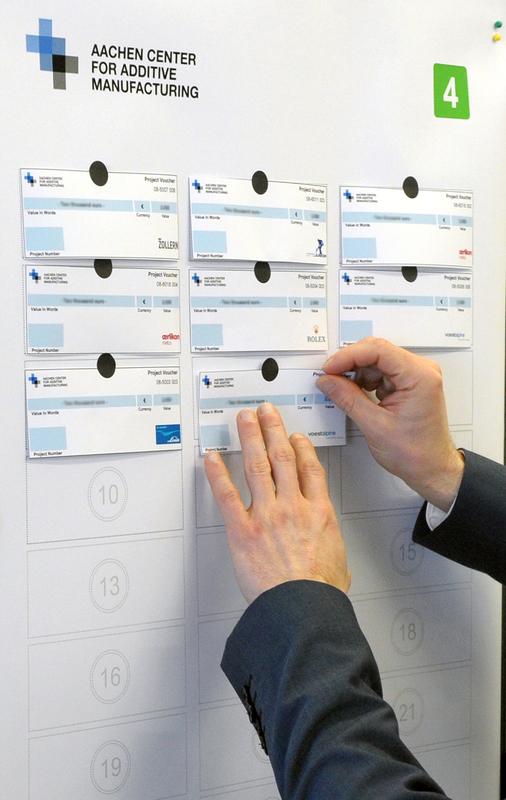
Route planner for the AM roadmap:16 new industrial partners agree a detailed training and research program during the first meeting of partners at the Aachen Center for Additive Manufacturing (ACAM).
Fraunhofer ILT, Aachen.
Tremendous reception by industry
ACAM partners produce a broad range of goods across many different industrial sectors – from gas and high-grade steel, luxury wristwatches, hybrid cars and tunnel boring machines, right up to aircraft and rocket engines. One of the reasons why ACAM GmbH has been given a tremendous reception by such internationally renowned companies as Rolex, IHI, Linde, Toyota, Zollern, Otto Fuchs, Mitsubishi and voestalpine is the great number of presentations that it has given at all kinds of events, from Formnext 2015 through to a project meeting of the EU’s HORIZON 2020 Framework Program.
In collaboration with the Aachen research network, which has come together to form ACAM GmbH, the 16 industrial partners are tackling the topic of additive manufacturing (AM) from every angle – ranging from projects on issues relating to design, process and business management; further education; feasibility studies and consultancy; through to the development of know-how in the expert community.
Both of ACAM’s managing directors, Dr.-Ing. Kristian Arntz (Fraunhofer IPT) and Dr.-Ing. Johannes Witzel (Fraunhofer ILT), have proposed initial joint research projects, and these will represent important pathways on the AM roadmap.
Launch with six research projects
The ACAM partners received vouchers worth a total of 154,000 euros, with which they selected six out of nine potential projects. These projects reflect the holistic nature of networking, since a great many issues are being addressed. These range from the demands on AM-based industrial process chains, the analysis and assessment of production facilities, the qualification of materials for LMD and SLM processes, through to the handling of metal powder and questions relating to health and safety at work.
A broad range of seminars for beginners and professionals
The seminars on offer will be equally broad-ranging. They will begin in May, in conjunction with ACAM’s research partners, and are aimed at AM beginners and experienced practitioners alike. The twelve seminars will last between one and several days, and they will cover areas such as the basics of additive manufacturing, the practical use of standard CAD software, AM-compatible design, and the opportunities for additive manufacturing in the casting industry.
A particular highlight is the Additive Manufacturing Innovation Day (June 23, 2016), when experts from KEX Knowledge Exchange AG (a professional technology and market information provider), the INC Invention Center (RWTH Aachen Campus), and Fraunhofer IPT will try out new AM ideas with ACAM partners in a playful environment.
Although the project is already underway, the network is not a closed community for insiders only. Ingrid Roll, who is responsible for Marketing & Community Management at the Aachen Center for Additive Manufacturing GmbH (ACAM), stresses this point: “ACAM is a growing enterprise, and it goes without saying that it is open to further partners.”
Companies can join the ACAM community as partners, for which the annual costs vary according to the membership model chosen: 12,000 € (Basic), 40,000 € (Business), or an agreed price based on an individually negotiated package (Cooperation). The following companies are already involved:
Concept Laser GmbH, Lichtenfels
Ferdinand Bilstein GmbH + Co. KG, Ennepetal
GKN Sinter Metals Engineering GmbH, Radevormwald
IHI Corporation, Tokyo (Japan)
IXUN Lasertechnik GmbH, Aachen
Linde AG, Munich
LUNOVU GmbH, Herzogenrath
Mitsubishi Heavy Industries, Ltd., Tokyo (Japan)
Oerlikon Metco, Winterthur (Switzerland)
Otto Fuchs KG, Meinerzhagen
Otto Junker GmbH, Simmerath
Rolex SA, Geneva (Switzerland)
Schaeffler Technologies AG & Co. KG, Herzogenaurach
Toyota Motor Corporation, Toyota City (Japan)
voestalpine Edelstahl GmbH, Vienna (Austria)
ZOLLERN GmbH & Co. KG, Sigmaringendorf-Laucherthal
You can find more information on our homepage: www.acam-aachen.de
http://www.ilt.fraunhofer.de/en.html
http://s.fhg.de/SEO