
Sewage Sludge Incineration Plant Powers Itself with Energy
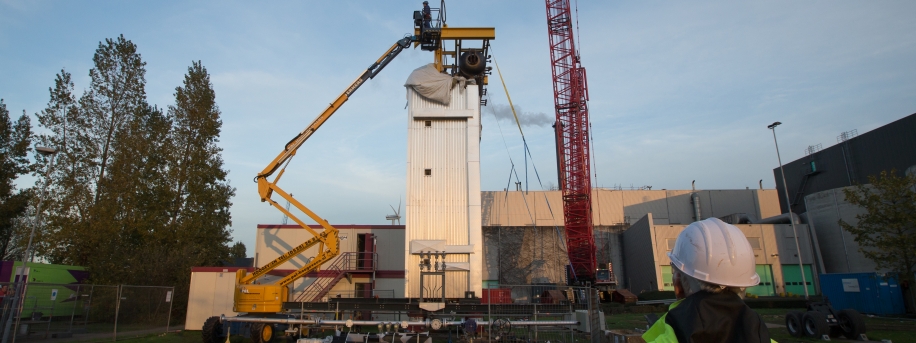
The boiler is ready to be hoisted into the facility.
Until now, the plant only generated low-pressure steam from the waste heat. The steam is used in various processes and, to a limited extent, for power generation.
Boiler specialist NEM, owned by Siemens and operating under its own brand, has now replaced two of the four low-pressure steam boilers with high-pressure boilers and has installed a turbine that generates electricity via a generator. This makes it possible for the operator to use the exhaust heat much more efficiently and produce nine times more power than before.
Recovering Raw Materials
In Germany alone, about eight million tons of dewatered sewage sludge accumulates every year. Around one third of the sludge is used for agriculture, a share that has stagnated for years due to the increased quality requirements for sewage sludge.
Incineration is therefore becoming increasingly attractive, either in specialized plants or as additional fuel in cement plants, coal-fired power plants, and waste incineration plants. Dedicated plants that only incinerate sewage sludge offer the advantage that valuable raw materials contained in the sludge, particularly phosphorous, can be separated and reused as fertilizers.
In the Netherlands, N.V. Slibverwerking Noord-Brabant (SNB) operates this type of dedicated plant and processes approximately 450,000 tons of dewatered sewage sludge every year. The dried sludge is incinerated at a temperature of approximately 900 degrees Celsius.
Waste heat is used more efficiently and phosphorous is recovered as fertilizer
Customized Boiler
When the SNB plant was retrofitted with two high-pressure steam boilers for power generation, engineers from boiler specialist NEM, which became part of Siemens in 2011, faced two challenges. They had to design the boilers so they could fit into the plant, which was built in 1997. In addition, the boilers had to be installed as quickly as possible while the plant was in partial operation so as not to disrupt processing of sewage sludge.
Experts implemented a boiler that meets the specifications for the turbine (450 degrees Celsius steam temperature at a pressure of 60 bar) while also complying with prescribed restrictions for size and weight. They achieved this in part by using a smaller diameter for the boiler’s economizer tubes, which allowed them to reduce wall thickness and hence weight.
In addition, it was necessary to adjust the spacing of pipes in accordance with height restriction while at the same time taking into account the fouling characteristics of the fuel. Engineers had to pay special attention to the selection of steam temperature. Sewage sludge contains many different chemical elements, some of which corrode metal at very high temperatures. That’s why the steam temperature was limited to 450 degrees Celsius even though the boilers and turbine would be able to operate at higher temperatures.
The steam drives a Siemens SST 110 industrial steam turbine. The turbine has two modules connected in parallel. A high-pressure module is operated at a steam pressure of 60 bar. After this, a low-pressure module supplies the remaining steam in the form of process steam at a pressure of 2.5 bar.
This low-pressure steam is used primarily to dry the sewage sludge, which contains approximately 75 percent water upon delivery. Retrofitting with high-pressure boilers eliminated the steam motor operated with low-pressure steam that had previously been used to generate electricity with a 450-kilowatt generator. Instead, the plant now uses a 3.5-megawatt generator to cover nearly all of its power requirements.Bei der Nachrüstung der SNB-Anlage mit zwei Hochdruck-Dampfkesseln.
Norbert Aschenbrenner
Contact
Mr. Dr. Norbert Aschenbrenner
Editorial Office
Siemens AG
norbert.aschenbrenner@siemens.com
Mr. Florian Martini
Press contact
Siemens AG
florian.martini@siemens.com