
Cooling With Metal Muscles: The Future of Refrigeration
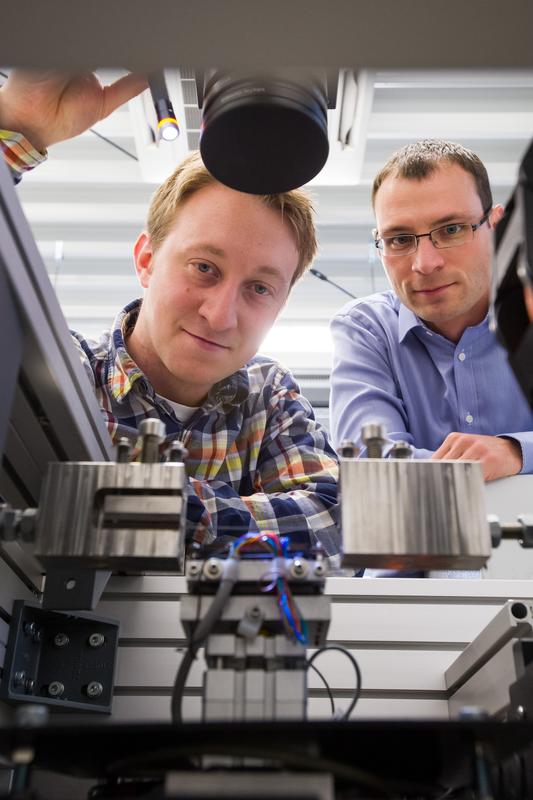
Engineers Marvin Schmidt (l.) and Johannes Ullrich from the research team headed by Professors Andreas Schütze and Stefan Seelecke are working on developing an environmentally sustainable and resource-friendly cooling method.
Photograph: Oliver Dietze
The approach taken by Professors Stefan Seelecke and Andreas Schütze from Saarland University focuses on systems that use shape memory materials, also known as ‘metal muscles’ or ‘artificial muscles’. Working together with researchers in Bochum, they are developing a new method of cooling in which heat and cold are transferred using ‘muscles’ made from a nickel-titanium alloy.
Extensive series of tests have yielded results that are now being used to develop a prototype cooling circuit that will be used to further increase the efficiency of the process.
The German Research Foundation (DFG), which has been funding the project for the last three years, has agreed to invest a further 500,000 euros. In total, the project has brought around 950,000 euros in funding to the region.
Cooling is carried out in all parts of the world. Refrigerators operate around-the-clock, air conditioning units cool offices, cooling systems help to keep computers and motors running smoothly. And the demand for cooling is being driven both by climate change and global population growth.
But more cooling systems come at a price – and not just a financial one. Increased cooling means increased consumption of electrical power and therefore higher emissions of greenhouse gases into the atmosphere, driving global warming even faster.
A more environmentally friendly cooling method has been developed by the research teams led by engineers Stefan Seelecke and Andreas Schütze in conjunction with the materials scientists Gunther Eggeler and Jan Frenzel at Ruhr University Bochum. The cooling process that they are developing does not require climatically harmful refrigerants and should consume less energy than the conventional cooling technologies used thus far.
‘In our systems, shape memory alloys (SMAs) are used to remove heat,’ explains Stefan Seelecke, Professor for Intelligent Material Systems at Saarland University. ‘Shape memory means that wires or sheets made from a nickel-titanium alloy have a certain ability to remember their original shape: If they undergo deformation, they will return to their earlier shape. So they are able to tense and flex like muscles. The fact that they absorb and release heat when they do so is something we exploit to achieve cooling,’ explains Seelecke.
If a nickel-titanium wire or sheet is deformed or pulled in tension, the crystal lattice structure can change creating strain within the material. This change in the crystal structure, known as a phase transition, causes the shape memory alloy to become hotter. If the stressed sample is allowed to relax after temperature equalization with the environment, it undergoes substantial cooling to a temperature about 20 degrees below ambient temperature.
‘The basic idea was to remove heat from a space – like the interior of a refrigerator – by allowing a pre-stressed, super-elastic shape memory material to relax and thus cool significantly. The heat taken up in this process is then released externally to the surroundings. The SMA is then re-stressed in the surroundings, thereby raising its temperature, before the cycle begins again,’ explains Seelecke.
In the experimental and modelling studies carried out so far, the researchers at Saarland University and the Center for Mechatronics and Automation Technology (ZeMA) in Saarbrücken have demonstrated that this type of cooling works and that it can be used in practice.
They used a model system to determine how to optimize the efficiency of the cooling process, examining such factors as how strongly the material has to be elongated or bent in order to achieve a certain cooling performance, or whether the process is more effective when carried out slowly or more rapidly. A thermal imaging camera was deployed to analyse precisely how the heating and cooling stages proceed.
‘We’re currently using these results to construct an optimized prototype for an air-cooling system. We are creating a cooling cycle in which hot air passes over one side of a rotating bundle of shape memory wires. Multiple wires are used in order to enhance cooling power. The bundle is mechanically stressed on one side as it rotates, thus heating up the SMA wires, as it rotates further the SMA relaxes and cools. The air to be cooled is guided past the cold wire bundle, thus cooling an adjacent space,’ says Professor Schütze from the University’s Measurement Technology Lab.
The team of engineers are currently fine tuning the process to optimize its efficiency. ‘Further optimization of the cooling process will involve modelling all component stages and then refining these models by comparing the predictions with experimental results. The data from the modelling and experimental work should allow us to determine the ideal number of shape memory wires for our rotating wire bundle as well as the optimum speed of rotation,’ explains Schütze.
Press photographs are available at http://www.uni-saarland.de/pressefotos and can be used free of charge. Please read and comply with the conditions of use.
Contact:
Saarland University
Prof. Dr. Stefan Seelecke: Tel.: +49 (0)681 302-71341; E-mail: stefan.seelecke@imsl.uni-saarland.de
Prof. Dr. Andreas Schütze: Tel.: +49 (0)681 302-4663; E-mail: schuetze@lmt.uni-saarland.de
Dipl.-Ing. Marvin Schmidt: Tel.: +49 (0)681 302-71347; E-mail: m.schmidt@lmt.uni-saarland.de
Ruhr University Bochum
Prof. Dr. Gunther Eggeler: Tel. +49 (0)234 32-23022; E-mail: gunther.eggeler@rub.de
Dr. Jan Frenzel: Tel. +49 (0)234 32-22547; E-mail: jan.a.frenzel@rub.de