
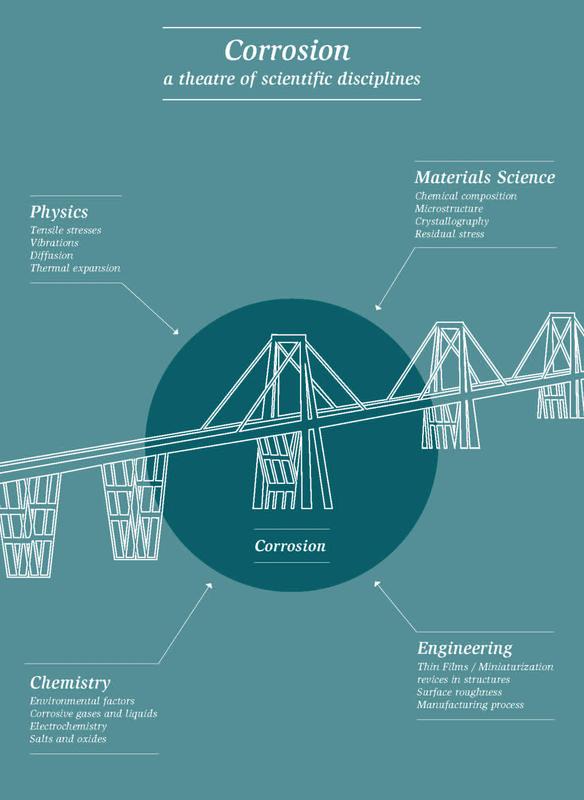
Corrosion - a theatre of scientific disciplines
Empa
The owner of a new Swiss industrial facility for the production of high-tech machinery was faced with a mystery: Kilometres of brand new stainless steel and aluminium pressure and cooling lines, worth several hundred thousand Swiss francs began to corrode while still under construction.
What had attacked the metals so quickly?
Empa experts took a close look at the entire system: Were corrosive building materials involved, were cleaning agents to blame or had the wrong materials simply been selected? Finally, they found the “culprit” in form of a small bottle on a workshop truck:
Instead of using a professional leak tester, the assembly team had used a universal cleaning agent from the supermarket to locate leaks with the foam. But the supermarket agent contained acids and chlorides that corroded the metals.
New scene: The caretaker of a school in eastern Switzerland notices corrosion on the ceiling lamp fixtures in the gymnasium during cleaning work during the 2019 spring holidays. The school administration consulted the architect who had supervised the construction at the time. He informs Empa.
The isolation cladding at the ceiling is dismantled. Result: The entire ceiling construction shows massive safety-relevant corrosion damage. A few years earlier, during the renovation, the workers had drilled metal hooks through insulation plates made of phenolic resin foam, being unaware about the material properties. Water condensation caused the insulation to become damp. The phenolic resin foam then developed strong acids, which caused the fixing hooks to rust throughout.
Engineer and Natural Scientist – Two Hearts in One Chest
Is such failure analysis the typical activity of corrosion researchers? Are they something like the pathologists of the construction industry who dissect corpses of material and are always looking for perpetrators?
Not at all. Corrosion researchers are much more than that. They work at the interface between materials science and construction on the one hand, chemistry and physics on the other. With one leg, they are engineers, with the other natural scientists. Further- more, they not only look at past mistakes – they also think of the future.
An example: hydrogen.
The aimed energy revolution will make it necessary to convert large quantities of excess electricity into hydrogen in the next few years. This is one way to store solar and wind power from summer until winter. However, this not only requires storage tanks, but also pipes, valves, nozzles, transport vehicles and various accessories, such as counters for the quantity of gas supplied.
All this must be made of high-strength steel that can withstand hundreds of atmospheres of pressure and be fitted with seals that prevent leaks for years to come.
How- ever, hydrogen penetrates some steels and leads to embrittlement of the steel even at normal ambient temperatures. At temperatures above 300 degrees Celsius, the hydrogen also chemically reacts with the carbon content of the steel and deteriorates its quality. Empa is already researching the mechanisms of hydrogen embrittlement and developing materials for the energy supply of the future.
Tracing Corrosion with Microsensors
Fatally, hydrogen is not only produced intentionally – it can also be formed during corrosion and penetrate the material. Stored in minute quantities, it has the same destructive effect there:
It makes high-tech alloys brittle and fragile. In order to understand what happens and how it can be prevented, researchers have to zoom in closely on the microstructure of a material and investigate the chemical reactions in tiny areas affected by corrosion.
Empa has developed its own microsensors that can analyse surfaces of less than one hundred thousandth of a square millimetre and detect less than one millionth of a percent by weight of hydrogen. Using these methods, they investigate critical zones in components, such as welded seams, which become brittle due to atomic hydrogen and could ultimately fail.
Lars Jeurgens has been leading the Empa laboratory for “Joining Technologies and Corrosion” since 2012 and, together with his team, maintains a well-balanced mix of research and industry-related services. “We have graduates from ETH Zurich and EPFL in our team and use the concentrated knowledge of these two leading engineering schools,” says Jeurgens.
He himself was born in the Netherlands and worked at the Max Planck Institute in Stuttgart for a long time. “Corrosion knows no boundaries – that's why we are very well connected internationally with experts from academia and industry and exchange the latest findings and methods. It is very valuable for us to share these experiences. Together, many complex problems can be solved more easily and quickly”.
Many Things to do
In addition, there is truly enough to do for the corrosion specialists. The automotive and aircraft industries, for example, are increasingly working with composite materials consisting of a wide variety of materials. Little is known about their corrosion behaviour in harsh operating environments.
In many places, alloys of iron, titanium and aluminium are also used. They owe their corrosion resistance to a tiny, nanometre-thin passive oxide film on their surface, which requires special analytical methods just to detect it – only then the material surface can be tailored for its corrosion resistance.
Finally, the application of functional coatings to miniaturized electronic devices and components raises new corrosion issues. Lars Jeurgens gives the following example:
“If I make a turbine with a corrosion-resistant coating and a hundredth of a millimetre of material thickness is lost every year, this is unproblematic. However, the same coating on an electronic device that is only one hundredth of a millimetre thick would be completely degraded within a year. What appears corrosion-resistant on a large scale is far from being so on a micrometre scale. We therefore need new concepts for classifying the corrosion sensitivity of a material for a given application.”
Corrosion – also in the Human Body
Sometimes corrosion occurs even where it is least suspected: In the middle of the human body, amidst its warm, apparently harmless body fluids. Empa's experts are investigating degradation by localized corrosion on materials such as stainless steel and titanium alloys, which are often used for implants as well as silicon, which is present in numerous new implanted components.
Little happens on large, smooth surfaces, but human body fluids can do a great deal in microscopically small crevices resulting from design or construction.
Recently, an Empa team was able to demonstrate the slow dissolution of a silicon-bonding layer in the laboratory. Between the titanium implant and the wear resistant coating a microscopic crevice may form. In the absence of oxygen, a very aggressive medium can develop there slowly, which can then destroy the silicon-bonding layer with the help of the body's own phosphorus compounds.
Using special probes, Empa researchers are also able to elucidate the local corrosion chemistry in such fine crevices and even accelerate the corrosion processes for experimental purposes. In this way, the expected service life of an implant can be predicted quite accurately even before the operation.
Corrosion research is enormously important in many real-life applications, and yet the work of the “pathologists of the engineering world” is often still underestimated. Lars Jeurgens and his colleagues are working hard to reinforce the importance of expertise in this field at universities and technical colleges.
“Corrosion assessment belongs on the checklist for every building project and every product development – not only at the end, but already during the drawing board phase,” says Jeurgens. “Oftentimes, we are only asked for an analysis when the colour brochures for their product have already been printed. But at that point, we are often unable to do anything for our clients anymore.”
Dr. Lars Jeurgens
Head of Laboratory “Joining Technologies and Corrosion”
Phone +41 58 765 4053
Lars.Jeurgens@empa.ch
Dr. Markus Faller
Chemical and Environmental Corrosion, Chemical Analytics of Corrosion Products, Corrosion-related Failure Analysis
Phone +41 58 765 4236
Markus.Faller@empa.ch
Dr. Martin Tuchschmid
Corrosion in Civil Engineering, Corrosion Management, Mobile Materials Analytics
Phone +41 58 765 4771
Martin.Tuchschmid@empa.ch
Dr. Patrik Schmutz
Corrosion research on light metals and medical products, Electrochemistry, Surface Analysis
Phone +41 58 765 4845
Patrik.Schmutz@empa.ch
Dr. Thomas Suter
Hydrogen-embrittlement, Local Electrochemistry
Thomas.Suter@empa.ch
https://www.empa.ch/web/s604/corrosion-slow-decay
https://www.empa.ch/web/s202