
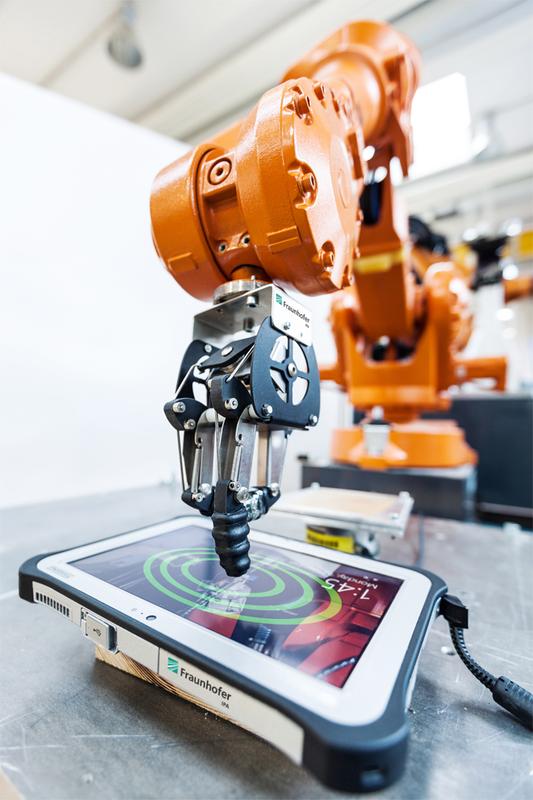
The developed robot system is capable of simulating thousands of typical usage scenarios on any kind of device with a human-machine interface, such as a touchscreen.
Source: Fraunhofer IPA/Photo: Rainer Bez
Thousands of repetitions in the space of just a few days: while manually impossible, this can be accomplished by a newly developed robot system from Fraunhofer IPA. Whether it’s a matter of pressing keys, inputting data or using fingers or a stylus, e.g. for a signature pad – the robot system is capable of realistically simulating typical applications of human-machine interfaces.
Such a system can test how long the materials human-machine-interfaces are made of and the associated functions remain fully functional. This provides device manufacturers with accurate knowledge about the quality of their products, which is, moreover, of importance for possible warranty claims. In addition, customers can gain accurate information on durability.
Robot imitates typical usage with its forces and path
For each device, the scientists collaborate with the manufacturer to first draw up the typical usage scenarios and loading profiles and to set up the robot system. This includes, in particular, setting up the end effector, which is capable of holding a variety of tools – similar, for example, to a finger or stylus – and simulating various loading scenarios.
The programming of the robot system depends on features that describe the interaction performed by the user on the devices with human-machine interfaces. The scientists measure these features in authentic situations with test subjects. That could include the duration and force registered during the interaction. If the device under test is a touchscreen, it might also be relevant where the action is typically performed. This data is used by the scientists to suitably configure the forces and path of the robot.
“We’ve succeeded in setting up the robot system so that it is capable of accurately simulating an application such as the use of a cash machine. Force sensors in a robot-guided finger-like end effector accurately measure and evaluate the force exerted by the user in a multiplicity of interaction cycles,” explains Milad Geravand, research assistant at Fraunhofer IPA. The accuracy of the tests is guaranteed by measuring systems as well as by regular checks by the employees.
Uniform quality of testing
“For a device manufacturer, automated testing offers the advantage that the performed conditions are always identical and the test scenarios are reproducible and therefore comparable. The motion of the robot system can be precisely controlled to guarantee that the testing is completely traceable and verifiable,” says Geravand. By the end of each intense test, device manufacturers are provided with a detailed report on the tests and results as well as with a brief summary, which can also be used as a reference for customers. The scientists are ready to employ this technology for life-cycle evaluation of human-machine-interfaces either in the labs at Fraunhofer IPA or on the manufacturer’s site by setting up the testing systems.
Expert contact:
Milad Geravand; 0711-970 1191; milad.geravand@ipa.fraunhofer.de
Press and Public Relations
Jörg-Dieter Walz | Phone +49 711 970-1667 | presse@ipa.fraunhofer.de | Fraunhofer Institute for Manufacturing Engineering and Automation IPA | Nobelstrasse 12 | 70569 Stuttgart
http://www.ipa.fraunhofer.de
http://www.ipa.fraunhofer.de/roboter_testet.html