
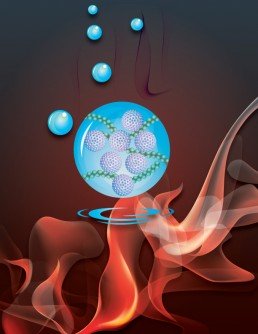
Credit: Jennifer M. McCann/MRI
An artistic interpretation of the cold sintering of ceramic particles (white) and polymer strands (green) using low heat to evaporate added water molecules (blue).
Ceramics is the oldest known man-made material, dating back tens of thousands of years. Throughout that time most all ceramics have been made by heating them to high temperatures, either by firing in kilns or sintering ceramic powders in furnaces, both of which require large amounts of energy.
“In this day and age, when we have to be incredibly conscious of the CO2 budget, the energy budget, rethinking many of our manufacturing processes, including ceramics, becomes absolutely vital,” said Clive Randall, professor of materials science and engineering at Penn State who developed the process with his team. “Not only is it a low temperature process (room temperature up to 200 degrees Celsius), but we are also densifying some materials to over 95 percent of their theoretical density in 15 minutes. We can now make a ceramic faster than you can bake a pizza, and at lower temperatures.”
In a recent article in the journal Advanced Functional Materials, Randall and his coauthors describe the co-sintering of ceramic and thermoplastic polymer composites using CSP. Three types of polymer were selected to complement the properties of three types of ceramics, a microwave dielectric, an electrolyte and a semiconductor, in order to highlight the diversity of applicable materials. These composite materials demonstrate new possibilities for dielectric property design, and both ionic and electronic electrical conductivity design. These composites can be sintered to high density at 120 degrees C in a time frame of 15 to 60 minutes.
Just add water
According to the researchers, the process involves wetting ceramic powder with a few drops of water or acid solution. The solid surfaces of the particles decompose and partially dissolve in the water to produce a liquid phase at particle-particle interfaces. Adding temperature and pressure causes the water to flow and the solid particles to rearrange in an initial densification process. Then in a second process, clusters of atoms or ions move away from where the particles are in contact, which aids diffusion, which then minimizes surface free energy, allowing the particles to pack tightly together. The key is knowing the exact combination of moisture, pressure, heat and time required to capture the reaction rates so the material fully crystallizes and gets to very high density.
“I see cold sintering process as a continuum of different challenges,” Randall said. “In some systems, it’s so easy you don’t need pressure. In others you do. In some you need to use nanoparticles. In others, you can get away with a mixture of nanoparticles and larger particles. It really all depends on the systems and chemistries you are talking about.”
The Penn State team has begun building a library of the precise techniques required to use CSP on various materials systems, with 50 processes verified to-date. These include ceramic-ceramic composites, ceramic-nanoparticle composites, ceramic-metals, as well as the ceramic-polymers discussed in this paper.
Other areas that are now open to exploration by CSP include architectural materials, such as ceramic bricks, thermal insulation, biomedical implants and many types of electronic components.
“My hope is that a lot of the manufacturing processes that already exist will be able to use this process, and we can learn from polymer manufacturing practices,” Randall concluded.
Co-authors on “Cold Sintering Process of Composites: Bridging the Processing Temperature Gap of Ceramics and Polymer Materials” were postdoctoral scholars Jing Guo and Hanzheng Guo, Ph.D. candidate Seth Berbano, research and development engineer Amanda Baker, and Michael Lanagan, professor of engineering science and mechanics, all part of Penn State’s Materials Research Institute.
The work was supported by the National Science Foundation as part of the Center for Dielectrics and Piezoelectrics and the NSF-ERC ASSIST program, the 3M Science and Technology Fellowship and the Department of Energy GATE Fellowship.
Contact
Prof. Clive Randall at car4@psu.edu